
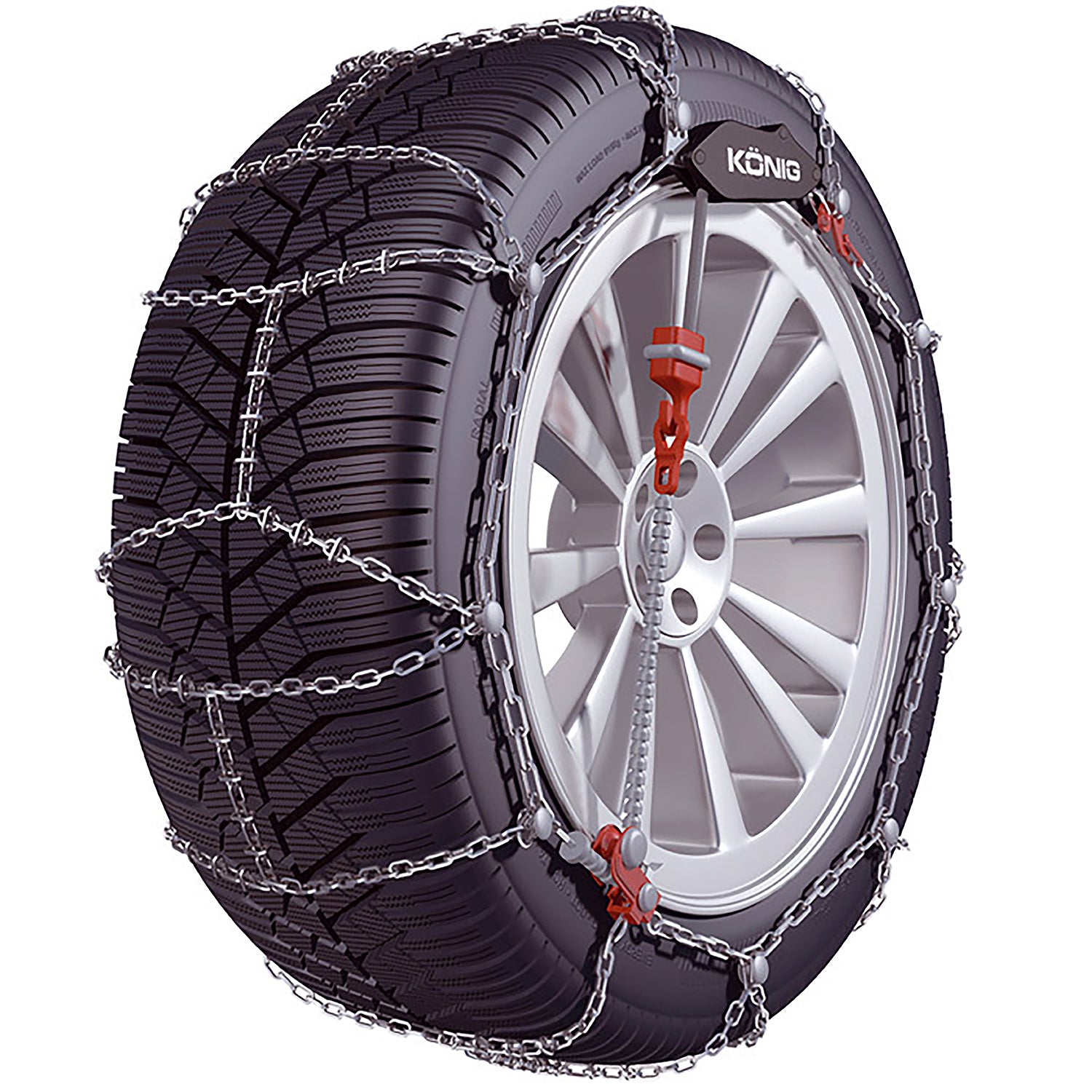
This application method employs a powder spray booth, powder feeder, electrostatic spray gun, and, depending on the type of gun used, a power unit.

However, some of the steps that are commonly employed during this stage include cleaning, rinsing, etching, blasting, and drying, and the most widely used equipment includes wash stations, blast rooms, and dry-off ovens. A complete preparation treatment is mainly dependent on the material being coated. If a surface is not sufficiently prepared, any remaining residues and deposits could affect the adhesion of the powder and the quality of the final finish.
Powdercoated konig backbone free#
Preparation Stageīefore the application of any powder coating material, the surface of the substrate must be cleaned and treated to ensure that the part is free of dust, dirt, and debris. There are three stages: surface preparation, coating application, and heat curing. During the process, the powder is applied to a substrate’s pretreated surface, melted, and then dried and hardened into a protective/decorative coating.

In contrast to the liquid coating process, which utilizes a liquid coating suspension, powder coating is a dry finishing process that employs powdered coating material. Overview of Powder Coat Process and Equipment The method includes a preparation, application, and curing stage, and, at a minimum, utilizes a spray gun, spray booth, and curing oven. Powder coating is a multi-step surface finishing process suitable for metal and non-metal substrates. Additionally, the article explores the benefits and limitations of the process and provides some of the considerations manufacturers must keep in mind when choosing a coating service provider.
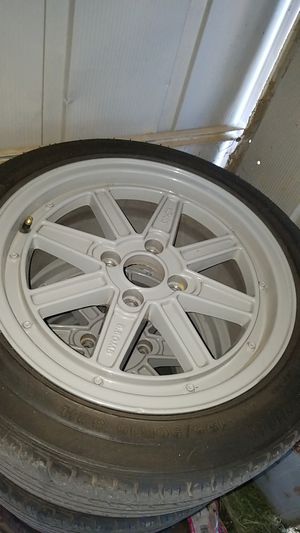
While each coating process has its advantages and disadvantages, this article focuses on powder coating, outlining the basics and the necessary components and mechanics of powder coating technology. The requirements and specifications demanded by a particular powder coat-e.g., application environment, substrate materials, sizing, costs, turnaround times, etc.-help determine the type of coating process most suitable for use. However, while powder coatings demonstrate some advantages over liquid coatings, especially in thick or high-traffic coating applications, they are not suitable for all manufacturing applications, such as for thin film or large part coatings. Either process can produce an even, hard finish which is generally more durable, cost-effective, and environmentally friendly than a comparable liquid coating. There are two main methods of powder coating-electrostatic spray deposition (ESD) and fluidized bed application. This finishing process is suitable for various materials, including metals, plastics, glass, and medium-density fiberboard (MDF), and can provide both functional and decorative surface coatings in a wide range of colors, finishes, and textures that are not readily achievable by conventional liquid coating methods. Powder coating is a finishing process in which dry, free-flowing, thermoplastic, or thermoset powder material is applied to a surface, melted, and hardened into an even coating.
